Should you calibrate your new equipment?
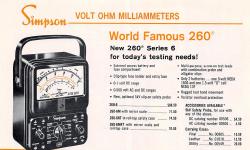
Does newly purchased equipment require calibration? The short answer is “yes.” (May we suggest you consider drop shipping new equipment to our laboratory for calibration.) We field this question quite often. Relax and read no further unless you need to know the reasons why.
Often, we are asked this question by a time-pressured technician in a desperate voice who has just purchased new replacement equipment to remedy a work delay. And just as often, before we can answer the first question, we are also hypothetically asked, “This equipment is brand new. Surely it is good, or it would have failed quality checks before it left the factory. I really don’t need to waste money having this calibrated, do I?”
Unreservedly, the answer is still “Yes, you need to calibrate your new equipment” even though the cost of calibration is not the real issue, it is the time cost of work delays. The stressed-out technician has made a couple of huge assumptions: (1) the supplier checked the equipment before it was shipped, and (2) the quality check was reliable. Neither of these situations is guaranteed to be true. Even though much new equipment contains a slip of paper with a number stamped on it that broadly states “Inspection Passed,” further reading will also say the equipment is limitedly warrantied against manufacturing defects. Read on, the manufacturer will only cover the cost of replacing the unit purchased. These sheets of paper are not “Certificates of Calibration” or “Calibration Reports.”
Keep in mind, many instruments are manufactured by unknown companies irrespective of what brand name they carry in your market, perhaps in jurisdictions with different standards allowing for errors much wider than the buyer’s. New measuring equipment is frequently placed into service straight from the box, most often with few problems. But that piece of paper with the comforting “Passed” stamp—it is free to the buyer, but when the user discovers an issue, the remedy will be far from free.